The Skills Gap and Industry 4.0
According to a report, India will be the youngest country in the world with an average age of 29 years by 2020. With such a young and robust workforce, there’s an excellent opportunity for India to boost its GDP and be on par with countries like the US, UK, and China in terms of economic growth. However, the sad truth is that more than 5% of Indians are unemployed, which stands at a whopping 40 million people without jobs and even more toiling with underpaid jobs.
The prime reason for this growing predicament can be the poignant skill gap which is taxing for businesses, employees, and the country as a whole.
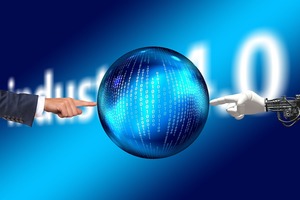
What Causes the Skill Gap?
Skill gap can be defined as the disparity between the skills a candidate possesses and the skills a particular position or an industry requires.
We have witnessed substantial advancements in technology in the last two decades. While this has generated more jobs, it has also resulted in the demandment of an improved skill set. However, the education system and curriculum hasn’t evolved much. Our antediluvian curriculum continues to produce individuals who lack the skills and competency required to meet the needs of an organisation.
According to a study, the number of engineering graduates who pass out each year is close to 1.5 million. The heart-breaking part is that only 7 percent of this youth can truly be deemed as employable.
There are many vacancies which remain unfilled due to the lack of employable candidates possessing the skills needed to fill that position. This has led to the creation of an environment of discontent for the youth, as well as for the businesses.
Concern Developing The Talent Pipeline
To bridge the skill gap, a new practice known as Talent Pipeline Management is being employed by certain businesses where the employers identify potential employees at an early stage. After the identification of candidates talented enough to meet the company’s expectations, the company stresses upon developing the skills of such candidates for employment in the future.
Though, Talent Pipeline Management seems to be a futuristic approach when it comes to bridging the skill gap, the picture is not all rosy. Firstly, the newly recruited candidates lack the necessary work-experience required to carry out the organisation’s work at a smooth and a steady pace.
Moreover, talent pipeline management can be quite a tedious task requiring careful identification of the company’s needs, extensive monitoring, and proper implementation. All of this requires both time and money.
Also, for the talent pipeline management to be executed immaculately, the company needs to work as a whole in order to develop the required skills in the identified individuals.
Sometimes, due to internal feuds in the company, proper skill development of newly employed candidates is not carried out properly. This can lead to a feeling of dissatisfaction amongst the newly recruited candidates.
Revolution in Industry 4.0
Industries today are going through a massive transition thanks to a host of new and coherent technologies like artificial intelligence (AI), the Internet Of Things (IOTs), and cognitive computing. These technologies have been developed in such a way that they can make logical and intelligent decisions without any human intervention whatsoever.
This shift is so colossal that it has been aptly termed as the 4th Industrial Revolution or Industry 4.0, which is believed to help boost the productivity of businesses and have a positive impact on the manufacturing, sales, machine safety, and IT security.
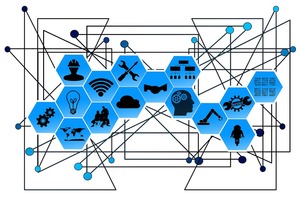
Impact of Industry 4.0 on Work-Organisation and Work-Life Balance
With artificial intelligence taking the driver’s seat, the manufacturing sector will get a boost with an error-free and an organised production process at lower costs.
Industry 4.0 will lead to greater customer satisfaction with the manufacturing process becoming more customer-centred with useful products being developed at a comparatively lower rate in order to meet the needs of individual customers.
There is an erroneous belief among the masses that the industrial revolution would lead to further unemployment with machines replacing the human workforce. This is not true because new advancements in technology will create fresh and more specialised jobs.
With the upcoming technologies, Industry 4.0 will need skilled individuals to deal with new technologies and work hand-in-hand with them for the growth of the organisation. The current situation is such that there is a serious dearth of skills needed to meet the needs of the jobs slated to sprout up in the future.
Industry 4.0 would also help create a better work-life balance. With advanced technologies, the workers would be able to work from wherever they desire. The concept of overtime and extra work hours would slowly diminish, thus, leading to an increase in the satisfaction level of the employees.
Industry 4.0 will also help the organizations get rid of tedious manual jobs which previously required a human workforce. The workers won’t be labourers anymore, but will instead be skilled supervisors who would efficiently co-ordinate the functioning of the machinery. This move towards Industry 4.0 will need existing labour to upskill.
Initiatives By the Government
1. Pradhan Mantri Kaushal Vikas Yojana
The skill gap has been estimated to put a whopping 1.9 trillion dollars of India’s growth at stake. To bridge the skill gap, the Government Of India has come up with an initiative known as the Pradhan Mantri Kaushal Vikas Yojana.
This scheme works by developing skills such as entrepreneurship, digital and financial skills among the unemployed youth. Individuals who possess any kind of previous learning experience are brought under a special category known as Recognition Of Prior Learning where they are trained according to the industry’s requirements.
2. SAMARTH
To keep up with the current pace of growth and development in the industry, the Government Of India has taken up an initiative known as SAMARTH (Smart Automated Manufacturing And Rapid Transformation Hub) with the establishment of four centres at IIT Delhi, CMIT Bengaluru and C4i4 Pune.
About C4i4
Based in Pune, the C4i4 centre is committed to promoting the adoption of advanced technologies like IOT, 3D printing, robotics, artificial intelligence, cloud computing, and cyber-security by Indian companies. This task is accomplished by educating the companies about new advances in technology through seminars and workshops.
C4i4 also runs various training programs to help the companies understand and integrate Industry 4.0 in their running. It is also helping the graduates upgrade their skills so as to match the needs of the Industry 4.0.
Kirloskar Centre Of Excellence
One size doesn’t fit all. Same is the case with Industry 4.0. Therefore, to make it more specific to the needs of the Indian companies and manufacturing sector, the Kirloskar group has set up the Kirloskar Centre of Excellence in Pune, aimed at Indianizing the Industry 4.0 so that the companies don’t fall into the trap of blindly copying the western implementation of Industry 4.0.
It also supports the ‘Make In India’ campaign by aiding the small and the big Indian manufacturing companies in understanding and implementing Industry 4.0 smoothly.
With the revolution in the industry and furtherance in the technology, the need of the hour is to up-skill and re-skill the existing talents with particular emphasis being laid on specialized skills like 3D printing and artificial intelligence. The companies, as well as the individuals need to take proper steps to bridge the skill gap. The companies can do their part by conducting regular training camps where the employees can gain knowledge as well as hands-on-experience when it comes to new advancements. The candidates, on the other hand can upgrade their talents by learning new skills and polishing their existing skills.